How to select the right cutting tool material when planning a successful metal cuting operation?
The selection of cutting tool material and grade is a critical factor to consider in a cutting operation.
A basic understanding of each cutting tool material and its performance is essential to making the correct selection.
Factors to consider when selecting a cutting tool material include the workpiece material to be machined, the component type and shape, machining conditions, and the level of surface quality required for each operation.
Coated Cemented Carbide Cutting Tool Material
Cutting tool inserts made of coated cemented carbide dominate the market. The exceptional qualities of this material, including high wear resistance, toughness, and the ability to be shaped into intricate forms, are the reasons for its popularity.
By coating cemented carbide with a custom grade, coated cemented carbide is produced, which is the preferred choice for various tools and applications.
Coating - CVD
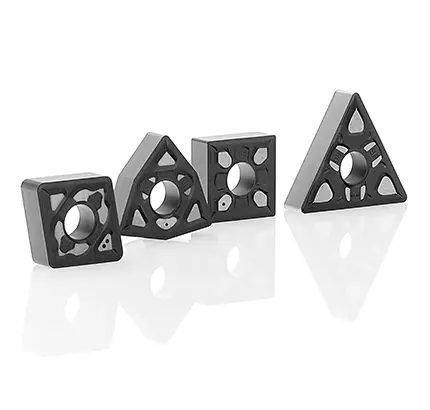
Chemical Vapor Deposition (CVD) is a process that generates coatings through chemical reactions at high temperatures (700-1050°C).
CVD coatings offer excellent wear resistance and adhesion to cemented carbide, and the first CVD coated cemented carbide was a single-layer titanium carbide coating (TiC).
Alumina (Al2O3) and titanium nitride (TiN) coatings were later introduced, and the more recent titanium carbonitride coatings (MT-Ti(C,N) or MT-TiCN, also known as MT-CVD) were developed to preserve the cemented carbide interface.
Modern CVD coatings combine these coatings (multilayer coatings), and their properties have been enhanced through microstructural optimization and post-treatments.
MT-Ti(C,N)- The material's hardness offers resistance against abrasive wear, leading to a decrease in flank wear.
CVD-Al2O3 - It exhibits resistance to crater wear due to its low thermal conductivity and chemical inertness. Furthermore, it enhances resistance to plastic deformation by acting as a thermal barrier.
CVD-TiN- This material enhances the ability to resist wear and is utilized for detecting wear as a top layer.
Post-treatments - Enhances toughness of cutting edge during interrupted cuts and mitigates smearing.
Applications:
CVD coated grades are preferred in various applications that require wear resistance, such as general turning and boring of steel, with thick CVD coatings providing resistance to crater wear. CVD grades are also suitable for general turning of stainless steels and for milling grades in ISO P, ISO M, and ISO K. In drilling, CVD grades are primarily used in the peripheral insert.
Coating - PVD
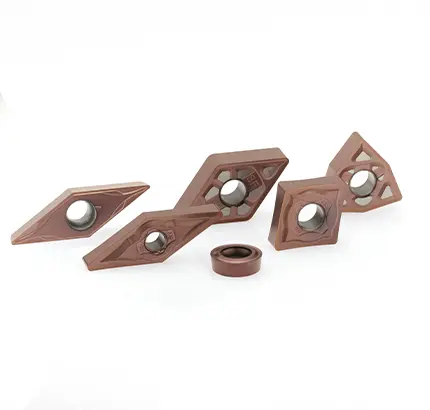
PVD coatings form at low temperatures (400-600°C) through the evaporation of a metal that reacts with nitrogen to create a hard nitride coating on the cutting tool surface. These coatings increase wear resistance and hardness of the grade, while their compressive stresses enhance edge toughness and prevent crack formation.
PVD-TiN-
The initial PVD coating was titanium nitride, which has a golden color and general-purpose properties.
PVD-Ti(C,N)- Titanium carbonitride provides increased flank wear resistance due to its greater hardness compared to TiN.
PVD-(Ti,Al)N-The combination of high hardness and oxidation resistance in titanium aluminum nitride enhances the overall wear resistance.
PVD-oxide- It is used for its chemical inactivity and superior resistance to crater wear.
Applications:
To achieve sharp cutting edges and handle smearing materials, PVD coated grades are recommended.
These grades are widely used for solid end mills, drills, grooving, threading, milling, drilling, and finishing applications, as well as being used as the central insert grade in drilling.
Cemented Carbide
Cemented carbide is a metallurgical material that is composed of powdery tungsten carbide (WC) particles and a cobalt-rich binder.
When used for metal cutting, cemented carbides contain more than 80% hard phase WC, and cubic carbonitrides are important components, particularly in gradient sintered grades.
The body of cemented carbide is created through powder pressing or injection molding techniques and then sintered to achieve full density.
Adjusting the hardness/toughness relationship of a cemented carbide grade is greatly influenced by the grain size of tungsten carbide (WC), finer grain size means higher hardness at a given binder phase content.
The grade's toughness and resistance to plastic deformation are controlled by the amount and composition of the Co-rich binder. More binder at equal WC grain size results in a tougher grade that is more prone to plastic deformation wear. Insufficient binder content may lead to a brittle material.
To increase hot hardness and form gradients, cubic carbonitrides or γ-phase are commonly added.Gradients merge improved plastic deformation resistance with edge toughness.
At the cutting edge, cubic carbonitrides are concentrated to enhance hot hardness, while a tungsten carbide-rich binder structure prevents cracks and chip hammering fractures beyond the cutting edge.
Applications:
Medium to coarse WC grain size, fine or submicron WC grain size and cemented carbide with gradient.
Uncoated cemented carbide cutting tool material
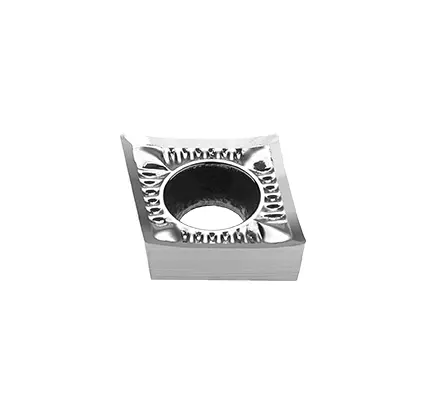
A small fraction of the cutting tool range comprises uncoated cemented carbide grades, which can be either pure WC/Co or contain a high concentration of cubic carbonitrides.
Applications:
This cutting tool material is commonly used for
machining HRSA or titanium alloys, as well as turning hardened materials at low speeds.
Uncoated cemented carbide grades exhibit a self-sharpening action and a controlled, yet rapid, wear rate.
Cermet cutting tool material
Cermet is a type of cemented carbide that consists of titanium-based hard particles, with the name cermet coming from a combination of ceramic and metal.
Originally, cermet was made up of TiC and nickel, but modern versions are nickel-free and have a specific structure consisting of Ti(C,N) core particles and a second hard phase of (Ti,Nb,W)(C,N), with a W-rich cobalt binder.
Ti(C,N) adds wear resistance, the second hard phase improves plastic deformation resistance, and the amount of cobalt controls toughness. Compared to cemented carbide, cermet has better wear resistance and less smearing, but lower compressive strength and thermal shock resistance.
Cermet can be coated with PVD for even greater wear resistance.
Applications:
The self-sharpening wear pattern of cermet grades makes them ideal for applications where built-up edge is a problem.
This characteristic helps to maintain low cutting forces even during extended periods of use, allowing for long tool life and close tolerances, as well as producing shiny surfaces in finishing operations.
Cermet grades are often used for finishing stainless steels, nodular cast irons, low carbon steels, and ferritic steels, as well as for troubleshooting in all ferrous materials.
Ceramic cutting tool material
A wide range of ceramic grades are available for different applications, all of which offer exceptional wear resistance at high cutting speeds.
Those ceramic grades are:
Mixed Ceramics
Mixed ceramics are toughened by adding cubic carbides or carbonitrides (TiC, Ti(C,N)) as reinforcing particles, resulting in improved thermal conductivity and toughness.
Oxide Ceramics
Aluminium oxide (Al2O3) forms the basis of oxide ceramics, which are strengthened by the addition of zirconia (ZrO2) to prevent cracks. This results in a chemically stable material, but it has poor thermal shock resistance.
Whisker-reinforced ceramics
To significantly improve toughness and allow for coolant usage, whisker-reinforced ceramics incorporate silicon carbide whiskers (SiCw). This type of ceramic is well-suited for cutting Ni-based alloys.
Sialon
Sialon (SiAlON) grades are well-suited for cutting operations on heat resistant super alloys (HRSA), as they offer both the strength of a self-reinforced silicon nitride network and improved chemical stability.
Silicon nitride ceramics
Silicon nitride ceramics (Si3N4) form a self-reinforced material with high toughness due to their elongated crystals. Although these grades are successful in grey cast iron, their use in other workpiece materials is limited due to their lack of chemical stability.
Applications:
The broad range of applications and workpiece materials for ceramic grades includes high-speed turning, grooving, and milling operations.
The specific properties of each ceramic grade, when applied correctly, enable high productivity.
Therefore, it is essential to understand when and how to use ceramic grades for successful machining.
Polycrystalline cubic boron nitride cutting tool material
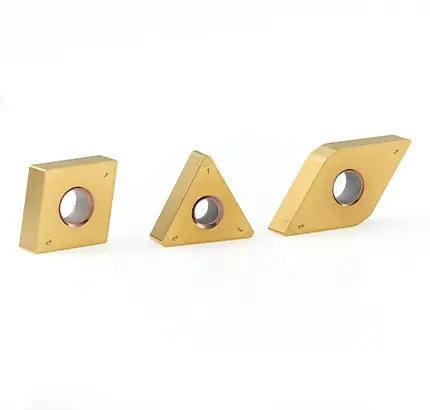
The cutting tool material known as polycrystalline cubic boron nitride (PCBN) offers excellent hot hardness, toughness, and thermal shock resistance, allowing it to be used at high cutting speeds.
Modern CBN grades are ceramic composites with a CBN content of 40-65%, and the ceramic binder enhances wear resistance.
High content CBN grades contain 85-100% CBN and may have a metallic binder for improved toughness.
CBN is typically brazed onto a cemented carbide carrier to create an insert, with vacuum brazing technology providing further bonding support for CBN cutting tips on negative inserts.
Applications:
CBN grades are commonly utilized for finishing the turning of hardened steels with a hardness of over 45 HRCe. At hardness levels exceeding 55 HRCe, CBN is the only suitable cutting tool that can replace conventional grinding methods.
Softer steels with a hardness below 45 HRCe contain a higher level of ferrite, which adversely affects the wear resistance of CBN.
CBN can also be used for high-speed roughing of grey cast iron in both turning and milling operations.
Polycrystalline diamond cutting tool material
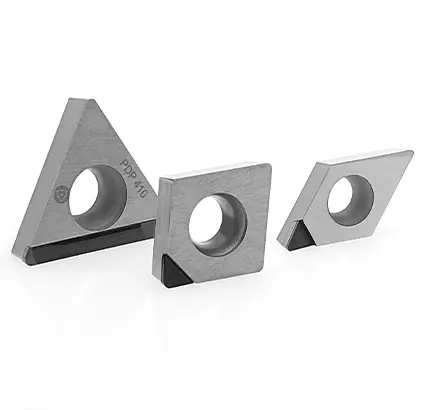
The PCD cutting tool material is composed of diamond particles sintered with a metallic binder.
Diamond is the most abrasion-resistant and hardest material available.
Despite its good wear resistance as a cutting tool material, it is prone to dissolving easily in iron and lacks chemical stability at high temperatures.
Applications:
The use of PCD tools is restricted to non-ferrous materials like MMC, high-silicon aluminum, and CFRP.
With the application of flood coolant, PCD can be employed for super-finishing of titanium.